Client and Application
BERICAP is one of the leading manufacturers of plastic closures for the beverage, food and industrial markets. The success story began in 1926. Bericap’s mission is to invent, develop, manufacture, market and consistently supply world-class high value-added plastic closures and dispensers, preferably with their own proprietary technology.
Bericap, located in Burlington, Ontario, had two plastic bottle cap recycling lines that needed to be upgraded and equipped with dust collection systems. The dust collection systems needed to match the following design criteria:
- Extract ground polypropylene bottle caps from the granulator and dump them into the gaylord
- Contain and filter the dust, and prevent it from escaping to the facility
- Comply with the Ontario Ministry of Labour, Ontario Fire Code and NFPA
Solution
The solution was to capture at source from the granulator chamber which was equipped with an air makeup pipe sized by AST. Clean fresh air is introduced via an 8”D heavy gauge pipe from outside in order to sweep the granulator chamber and transfer all the ground plastic particles to the dust collector. The dust collector has an integrated baffle and cyclone which separates the bigger particles from the fine dust. Large/heavy particles fall with gravity to the hopper and through a rotary airlock into the gaylord. The fine particles are filtered and captured by the dust collector main filter. The dust collector airflow rating is 1,100 CFM. The dust collector has a full VFD control panel which provides constant airflow regardless of the filter condition. This panel is also linked to the granulator control panel. The following are the details of the solution:
• The dust collector is grounded, and the heavy duty ductwork (schedule 10 pipe) electrically bonded to the collector.
• The collector is fitted with a Fike suppression system to prevent any explosion.
• Fike Suppression bottles are installed on the piping as isolation devices.
• A signal from any of the protection equipment will de-energize the fan and create an alarm.
• Transport velocities exceed 5,200 FPM.
• The production line is interlocked to the operation of the dust collector fan.
• Clean air is exhausted to the outside.
Equipment
The following equipment was installed in this project:
- Two (2) TD-573 cartridge filter dust collectors
- Two (2) PB-15A side-mounted 5HP TEFC pressure blower fans with silencers
- Two (2) 8” CI Rotary Airlocks
- Two (2) AST-CP-VFD-5HP-575V control panels
- Two (2) Fike Suppression systems
BERICAP Project Images
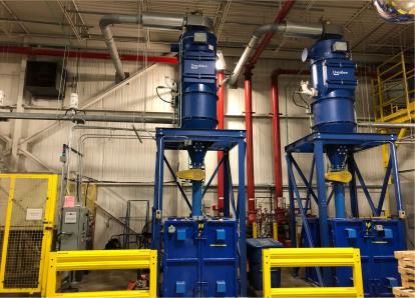
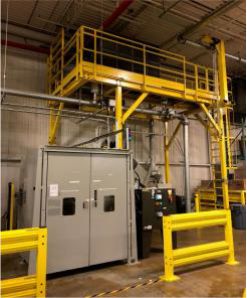
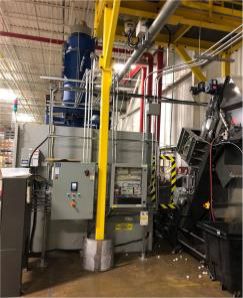
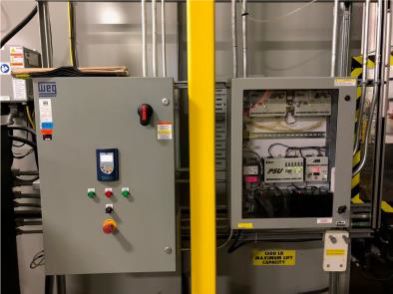
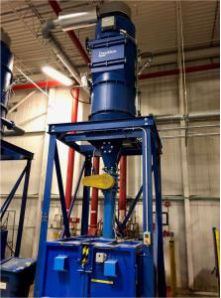
